Know Your Ready Mix Concrete in the Comox Valley
Ready mix concrete that has been properly poured, cured and protected will last longer than any other building material. It is the most multipurpose building material in the world. There are a number of elements that you should know about concrete including:
Curing Concrete
Curing concrete properly requires the correct control of moisture and temperature to achieve 100% of its potential design strength, and this is critical to the long-term durability. Concrete must be kept as moist as possible for the first seven days after placement and it must be allowed sufficient drying time before being subjected to freezing temperatures or to de-icing salts. The science related to the practice of a seven-day curing period is:
- Cement, the “active” ingredient in concrete requires constant moisture to gain strength.
- If concrete is kept moist for the seven-day period, it will gain strength, and will shrink less and produce fewer cracks.
Curing can be assisted in a number of ways:
- Spray-on liquid curing agents and sealers.
- Water ponding or spraying a mist over the concrete.
- Coverings such as wet burlap, polyethylene, insulating blankets, etc.
- Leave forms in place.
A liquid curing agent is the most effective and convenient method. The curing agent should be applied as soon as finishing is complete. Curing agents form a membrane on the surface in order to retain moisture. Once the curing agent has been applied, no further working of the concrete can be done. Use a spray or roller to apply curing agents.
According to CSA A23.1-09, (Canadian Standards Association) curing is a mandatory part of concrete construction and requires moisture to maintain the concrete at 100% relative humidity and a minimum temperature of 10°C for a period of at least 3 days. This period is extended to a minimum of 7 days for the durability requirements of exposure classes F1, C1, C2, S1, and S2.
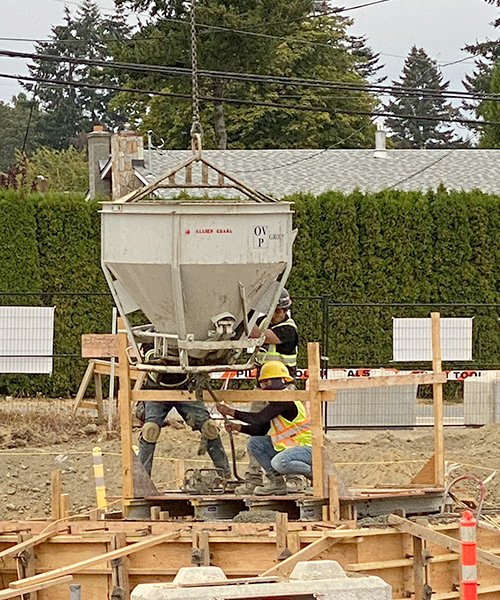
Hyland Precast is as a designated distributor of Redi-Rock® in British Columbia. We deliver precast modular blocks to Vancouver Island, Gulf Islands, Vancouver Coast & Mountains, Thompson Okanagan, Kootenay Rockies, Cariboo, Chilcotin and Northern BC regions.
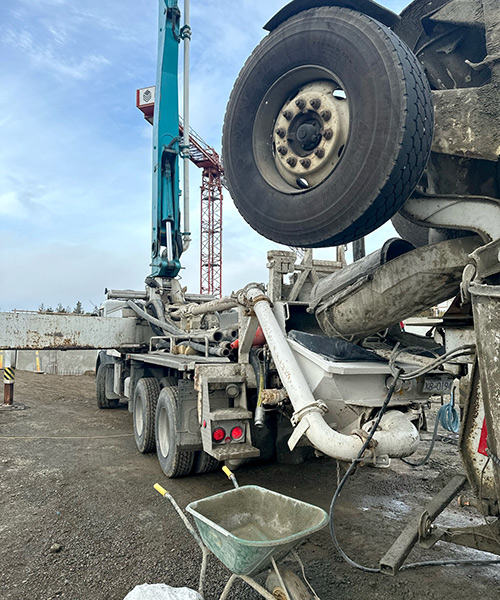
Cold-Weather Curing
Cold weather curing is defined as a period where average daily temperatures fall below 4º C for more than three consecutive days. Concrete can be placed safely throughout the colder months if precautions are taken. During colder weather, the mix should be adapted to the ambient temperature by heating the concrete, adding accelerators, and providing protection. On Vancouver Island, because of historical temperatures from November 1 through March 15, Hyland Ready Mix heats all concrete to meet the requirements of CSA and to maintain reasonable setting times and strength gain.
The temperature of concrete during and after placement is critical since concrete sets more slowly as the temperature drops. Hydration is affected by initial concrete temperature, ambient air temperature, the dimensions of the concrete and mix design. Concrete generates heat during hydration, the chemical process by which cement reacts with water to form a hard stable paste. Finishing and form removal should be delayed in cool weather and strength development can be impaired if appropriate precautions are not taken.
Do not place on frozen ground, on snow, or in freezing weather. If concrete freezes while in a saturated condition, surface problems like scaling, spalling or cracking can arise due to the expansion and contraction of frozen water inside the concrete. During freezing weather, water curing of concrete should be terminated 12 hours before the end of the protection period. Do not use a curing agent if there is any chance that the concrete will freeze during the curing period.
- Protect from freezing temperatures for 3 to 7 days after placing.
- Leave forms in place as long as possible. Corners and edges are most vulnerable (cover and heat if necessary).
- Protect flatwork by covering and heating, or using insulated blankets, or covering with plastic and straw.
This information has been provided to assist you with your cold weather construction. The complete standards guideline for concrete constructions is CSA A23.1-09 Section 21.
Superplasticizers
Superplasticizers are water-reducing admixtures that increase slump (a measure of consistency of freshly mixed concrete) to make concrete easier to place. Superplasticizers disperse particles of cement throughout a concrete mix. The effect is the same as adding water, but without the detrimental side effects. In addition, they reduce water in the mixture to gain higher, earlier strengths.
As a contractor, superplasticizers can help you to build more economically and to produce higher quality concrete at the same time, since moderately flowing concrete can be placed more easily providing good consolidation around rebar and tight forms with minimal vibration. Combine superplasticizers with low initial slump concrete to produce a workable mix with higher earlier strength.
Superplasticized concrete is great for floors, suspended slabs, toppings, walls, columns, and anywhere that higher slump concrete is required.
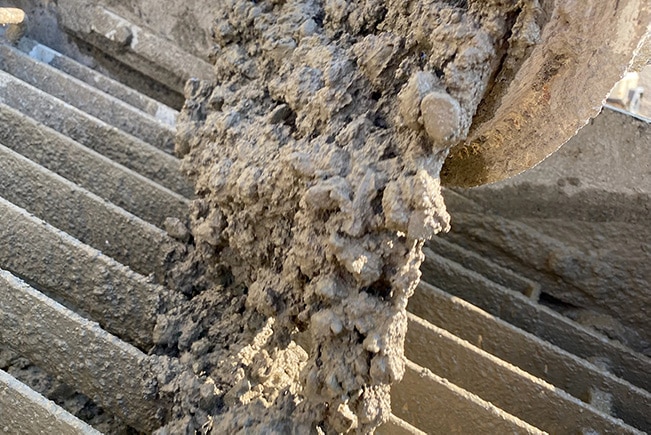
Sealing
After the concrete is fully cured, the application of a concrete sealer is highly recommended. The advantages of sealing concrete include:
- Improves appearance
- Makes surfaces easier to clean
- Provides protection against de-icing salts
- Resists mildew and surface staining
- Inhibits efflorescence (a whitish powder on the surface)
- Sealers should not be used on coloured flatwork.
Hyland Ready Mix News
Hyland Concrete Technical Bulletin – Pouring ready mix in hot weather
Hot Weather Concreting Considerations for Standard Concrete Applications What is considered hot weather? As per CSA A23.1-7.1.1 hot weather concreting occurs when the ambient ....Read More >>
The right way to pour concrete in cold weather
Build your winter concrete projects Whether you are a commercial contractor building a winter project, or a homeowner improving your property outdoors, the colder Vancouver ....Read More >>
The Comox Valley Water Treatment Plant – A year in review
This fall the Comox Valley Water Treatment plan celebrated one year of the construction completion. We thought it would be a great idea to ....Read More >>